Shop Log - 7/22/22
Picking up from where we left off last week, I not only finished sculpting all the parts for my beasty buck (and the head sculpt) but made silicone molds of all the parts as well.
.jpg)
I did an initial casting today using some brown pigmented
Flex-It 90 resin and while I couldn’t be happier with the arms and torso, I
think I have some more work to do on the head sculpt. I plan to resculpt parts
of the head to make the brows more detailed and possibly ditch the mouth full
of fangs and just give him a pronounced underbite like the Lon Chaney Jr Wolf Man.
I wasn’t expecting teeth to be so difficult to sculpt, but I think I know what
I can do better. But the biggest problem so far with this initial casting is
that he just doesn’t stand up without his display base. As you can see from the
picture above, the urethane resin master part from which I made the legs mold
can stand there just fine but when cast in my flexible resin and fully
assembled with the other parts, there was a weight distribution issue that made
the figure keep falling backwards. Part of this is due to the flexible resin
being considerably lighter than rigid urethane resins but I found that it was
mostly due to how I designed the feet.
I guess that is one drawback to making your masters/original
sculpts from urethane resin blanks. While it does provide a solid, stable (and easily
sandable) canvas from which to customize a figure part, it’s difficult to tell how
it will look and function after you mold it in silicone and cast it in resin (at
least for me, anyways). I did, however, add a quick black wash, Calvary Brown
dry brushing, and add a few other paint apps just to see how it would look. I
didn’t prep the figure or prime it with adhesion promoter or anything, I was
just curious to see if I felt better about the teeth and brows after if I painted
them. I didn’t.

And while I’ve yet to revise the head sculpt, I did get to
tinkering around with the legs and trying to get to the bottom of this weight
distribution issue that was preventing him from standing up. It’s hard to tell
from the pic below, but I added some globs of Green Stuff on and around the
feet on the initial legs casting (pictured on the right) until I came to the
conclusion that his feet were initially too flat and that was the source of all
the problems. Once fixed, I textured the Green Stuff to blend it in with the
rest of the fur as best I could and made yet another silicone mold using my
modified legs casting as the master part this time. Just like last time, I
build a mold box out of Lego and filled the bottom with chunks of leftover
silicone and bits of failed or retired molds to help save on fresh silicone. I’m
current down to my last two gallons of Cast-A-Mold 25 silicone, which is no
small amount but I still like to conserve as much as I can because there are
many, many more molds that I still plan to make.
At any rate, the newly retooled legs mold was ready for its
maiden resin pour by the time I finished work and here it is, the new set of
legs fresh out of the mold and attached to the figure. As you can see, my
efforts were a success and the figure can now stand on its own! Now I just have
to fix that face and we’ll be back in business.

And progress on my Mr. Boneface series is grinding along as
well, slowly but surely. Right now I’m still focusing on making his weapons
before moving on to his armor/soft-goods, then the prepping and painting, and
finally the packaging. And all of those things all have their own processes.
Creating a weapon, for instance, involved kitbashing said weapon from other
parts, then making a mold of that, then casting five copies of that (repeat
three times, since each of the three Mr. Boneface figures will come with its
own unique weapon).
Oh, and last time I forgot to show you what the tree mold
containing the random “base” weapons that I use to make unique weapons looked
like after I cast it in rigid urethane and take it out of the mold. I think it
looks pretty cool:
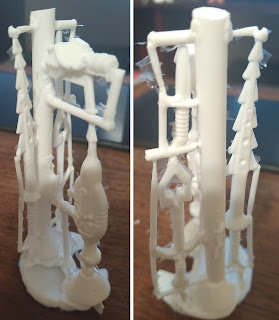
And this is what it looks like when all the parts are
snipped off the tree. It reminds me of building a snap-together model kit. And just
like last time, I chopped up some of these urethane-casted weapons to create a
new one for the next Mr. Boneface.

And here’s a pair of nunchaku that will come with the green
Toxic Slime Pit Mr. Boneface. I used two handles from that crazy lance-type
weapon and connected them with a length of jewelry chain that I had in my bits
box. In addition to nunchaku just being a fun weapon, something about those
handles really reminded me of Panthro’s nunchucks from the Thundercats. If
you’re keeping score, two of my three Mr. Bonefaces have custom weapons now (as
well as molds for those weapons). Now I just need to come up with a weapon for
my third Mr. Boneface (the one inspired by Skeletro from I, Mercenari), who I’m
thinking of giving a handheld scythe using that arrow-shaped short sword as a
base.
I should also note that this pair of ‘chucks is just a
prototype that was cast in the same brown as my initial werewolf/beasty buck
mold test/first-shot. I’m thinking the handles will be a more solid shade of
green to better match the figure. Also, when I’m casting the accessories for
each figure, I’ll probably do the stand/base and the weapon at the same time,
so they’ll both be the same color. I don’t think anyone will mind that and it
really saves me a step since cure time for this resin is 1.5 hours and I only
have one pressure pot. Plus, with the 3 minute working time for said resin, I
only have time to mix and pour (or rather, inject) one color of plastic for one
set of molds if I’m to get it into the pressure pot in time.

In the final bit of Mr. Boneface-related news for this Shop
Log, I finally got around to testing the water with the Flex-It 40 resin that I
plan to use to make the clothing-style accessories for my 5” scale figures (as
well as some custom keshi figurines if I have any of it left). I took this
bandolier accessory from another one of my random He-Man bootleg figures, made
a two-part silicone mold it, and filled it with some Flex-It 40 resin, and put
it in my pressure pot tight before sitting down to finishing writing this
article. What’s cool about Flex-It 40 is that it has a 15 minute working time,
making it a lot less hectic to work with than Flex-It 90 with its 3 minute
potlife. On the flipside, it takes five hours to cure whereas Flex-It 90 only
takes an hour and a half.
Suffice to say, I won’t know how this maiden voyage with
Flex-It 40 will turn out until tomorrow morning. What I’m really curious to
know is not only will it be flexible to fit over a figure and conform to its
curves like soft-good materials (like cloth or EVA foam) might, but also if the
clasp used to fasten both ends of the accessory will work. How well this
initial test turns out will determine the course of Mr. Boneface’s final
pack-in accessories and how soon I’ll be able to finish the figures and get them
listed on Etsy.

In addition to all the other stuff I cast in that same brown
plastic, I also had a mold set aside for two urethane resin head blanks that I
previously sanded down for later customizing (getting rid of the hair and some
other features to make it more of a blank slate). Since I can never have enough
blank heads to customize, I made a silicone mold of those two sanded-down head
sculpts and cast two initial copies in Flex-It 90 (because I ran out of white
urethane resin, though I can still probably work with these).
Because it’s a stiflingly hot day and not ideal for resin
casting, one of the heads didn’t fill up all the way but that’s okay. Since
I’ll be sculpting onto these heads with Milliput, Green Stuff, and Apoxie
Sculpt, that hole on the top of the head can easily be covered up.

And while we're on the topic of new head molds, I took a Hulk Hogan
head from a bootleg He-Man figure, made a mold of it, added a piece of a wooden
dowel to the bottom of a urethane resin casting from said mold, and made
another mold of THAT. This now gives me a Hulk Hogan head that I can fit on my
luchador/generic wrestler buck.

Here’s a test fitting on my first (and so far only) casting
from my set of wrestler molds. I look forward to doing a really out-there
series of five-inch wrestling figures (think something along the lines of
M.U.S.C.L.E. or the Monster In My Pocket wrestler series only they’re
articulated figures that are in this scale) but I want to get my Mr. Boneface
figures finished and out to market first.

And I did make some more progress with my custom Lone Ranger
figurine that I made from a urethane resin recasts of an old Louis Marx cowboy.
I painted the base and sealed it with a matte clearcoat before supergluing the
Ranger onto it. I went over the figure with a dry brush as well, going back
over the shaded areas it with the basecoat (Citadel Fang plus a few drops of
white) and leaving as much of the black wash in and around the folds as
possible.
I still have some touching up and highlighting left, I think (not to mention a final clearcoat). But we’re almost there
Comments
Post a Comment